Introduction
Quality control is at the heart of every manufacturing process. It’s a vital part of making sure every product meets the required standards before it reaches customers. Defective products cause financial losses, recalls, and, unfortunately, reputational damage. Quality assurance is especially critical for industries like automotive, pharmaceutical, and electronics.
Traditional quality control methods rely on manual inspections, which are slow, inconsistent, and prone to human error. Even rule-based detection systems struggle with microscopic or irregular defects, reducing overall quality assurance efficiency. As production demands increase, these limitations create bottlenecks that affect both product quality and operational costs.
Artificial intelligence (AI) and computer vision, which is a branch of AI that deals with visual data, are changing quality control for the better by automating tasks like defect detection. By finding patterns in images and videos, these technologies can identify defects instantly. This makes production faster, more accurate, and consistent. Such AI systems can adapt to different product materials, lighting, and product changes, making sure only the best quality products reach distribution centres.
With industries increasingly prioritising automation, the demand for AI-enabled quality control is rapidly growing. Many companies are already using or looking into adopting AI tools for quality control and maintenance. As a result of this growing popularity, the AI quality inspection market is projected to reach $70.7 billion by 2029. This also reflects the industry’s slow and steady shift toward AI automation. In fact, 64% of the manufacturing sector now relies on Industry 4.0 technologies like AI and cloud computing for operational improvements.
In this article, we’ll explore how AI, computer vision, generative AI, AR (augmented reality), VR (virtual reality) and XR (extended reality) are improving quality control and maintenance across various industries. We’ll also discuss some real-world applications of AI and emerging trends in quality assurance using AI.
Understanding Computer Vision in Industrial Applications
When it comes to quality control, AI and computer vision systems analyse visual data to detect defects in products with precision. This is an improvement over manual inspections, which can be slow and inconsistent. In fact, Vision AI systems can process thousands of images per second. It can identify flaws, misalignments, and structural defects that might go unnoticed by human inspectors. To achieve precision with respect to defect detection, these AI solutions generally apply different computer vision techniques at various stages of the quality control pipeline.
Also, image processing is a key part of these systems. It is used to adjust parameters like the contrast, sharpness, and brightness of visual data to improve detection accuracy under different lighting conditions. Using image processing for pre-processing enables AI models to receive clean, high-quality images for analysis. After that, techniques like image segmentation can divide images into multiple sections to help AI models identify defective areas in real time with greater accuracy.
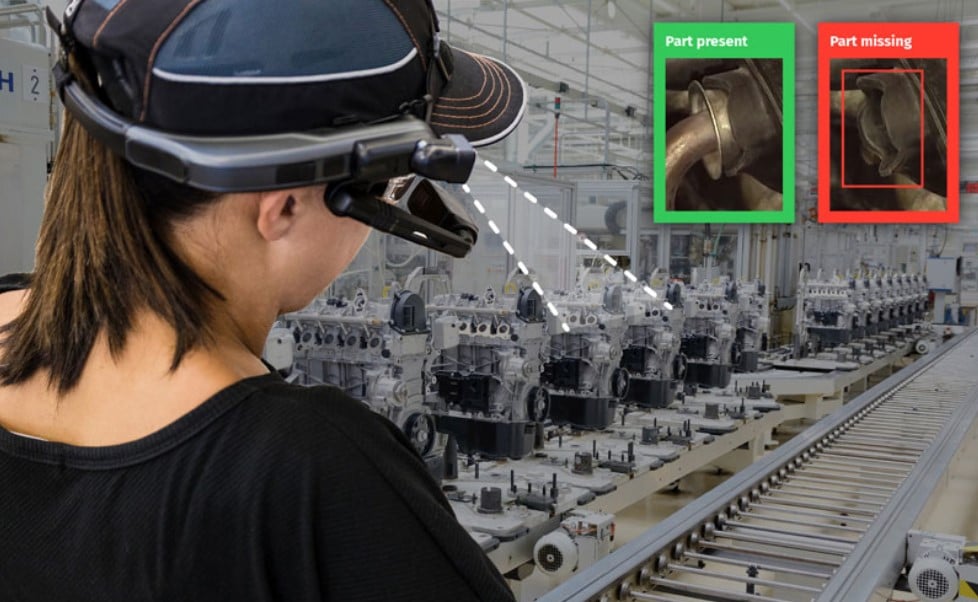
On top of this, object detection is used to identify missing, misaligned, or damaged components. At the core of these processes are Vision AI models like Convolutional Neural Networks (CNNs), RCNN, and YOLO. These models can extract and process visual features for accurate defect detection.
However, object detection isn’t limited to traditional CNN-based methods. Vision transformers are a newer approach that adapts transformer architectures, originally designed for processing language, to handle visual data. Instead of analysing an entire image at once, these models divide an image into smaller patches, processing them as a sequence to capture both local and global relationships.
While they can be a bit slower than conventional CNNs, their ability to extract more detailed and robust features means they could become increasingly valuable in complex tasks such as defect detection. For instance, foundation models like DINO have demonstrated strong performance in feature extraction, offering a promising alternative despite their heavier computational demands.
Real-World Use Cases of AI in Quality Assurance
Many industries using AI in quality control systems have seen an increase in defect detection, up to 90%. By using AI tools, they are also reducing waste and improving production efficiency. Let’s take a closer look at some real-world examples of industries using AI in quality control and maintenance.
AI Defect Detection in Automotive Production Lines
Many car manufacturers are already using AI to quickly detect scratches, dents, and structural deformities without slowing down production. AI-driven computer vision systems can scan car bodies in real time, spotting even minor defects that might otherwise be missed. It speeds up quality control and ensures that vehicles meet safety and design standards.
For example, leading automotive manufacturers like BMW and Audi have integrated computer vision systems into their production lines to detect surface defects on car bodies. Using Vision AI, they have managed to reduce manual inspection time by up to 50% and improve defect detection rates.
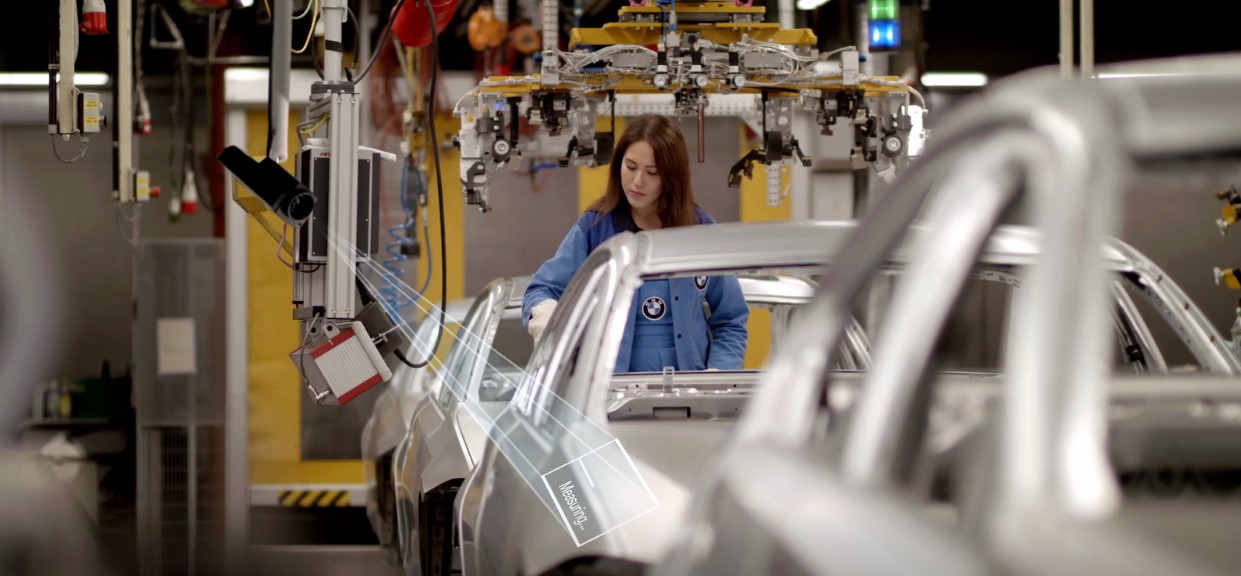
Generative AI in Industrial Operations
Generative AI is a subfield of AI used to create or generate new data like text, images, audio, and video from scratch. In quality control and maintenance, generative AI can be used to create synthetic failure scenarios, helping industries predict and prevent equipment malfunctions before they occur. Many companies are already looking into adopting Gen AI for such predictive maintenance practices. In fact, the market for generative AI in manufacturing is projected to grow significantly, reaching $13.8 billion by 2034.
Manufacturing plants can collect vast amounts of operational data through different sensors. This data can be used by generative AI systems to create different failure possibilities. Insights from these scenarios can optimise maintenance schedules and improve system reliability. It is usually used with digital twin technology, where AI can be used to create virtual versions of machines. It helps detect problems early and improve performance before issues arise.
For example, let’s say there’s a robotic arm on an assembly line. Sensors can continuously monitor its temperature, vibration, and motor currents. Generative AI systems can use this real-time data to simulate potential failure scenarios, such as overheating or mechanical wear under different operating conditions. By testing these scenarios on a digital twin of the robotic arm, engineers can detect early signs of potential issues, adjust maintenance schedules accordingly, and implement timely repairs.
Using XR for Remote Quality Inspections
Extended reality is a technology that combines both augmented reality and virtual reality VR. XR can be used to monitor quality control operations remotely from anywhere. Using XR for remote quality inspections removes the need for extensive physical testing. Doing so reduces operational costs and improves workflow efficiency. As industries continue adopting AI and computer vision, XR-based inspections are set to become a standard in aerospace, manufacturing, and other high-precision industries.
Using AI, XR can add digital details to real-world objects, helping inspectors spot defects, structural issues, and inconsistencies more accurately than before. Today, 88% of XR companies use AI, showing a move toward smarter and more automated systems.
These systems use high-resolution cameras and AI-based image analysis to detect even the smallest anomalies. This combination increases the speed of performing inspections, reduces human errors, and maintains consistent quality standards across industries.
For example, Boeing has implemented AR for aircraft maintenance. AR helps technicians to view digital schematics overlaid on aircraft components, reducing inspection time by 40%.
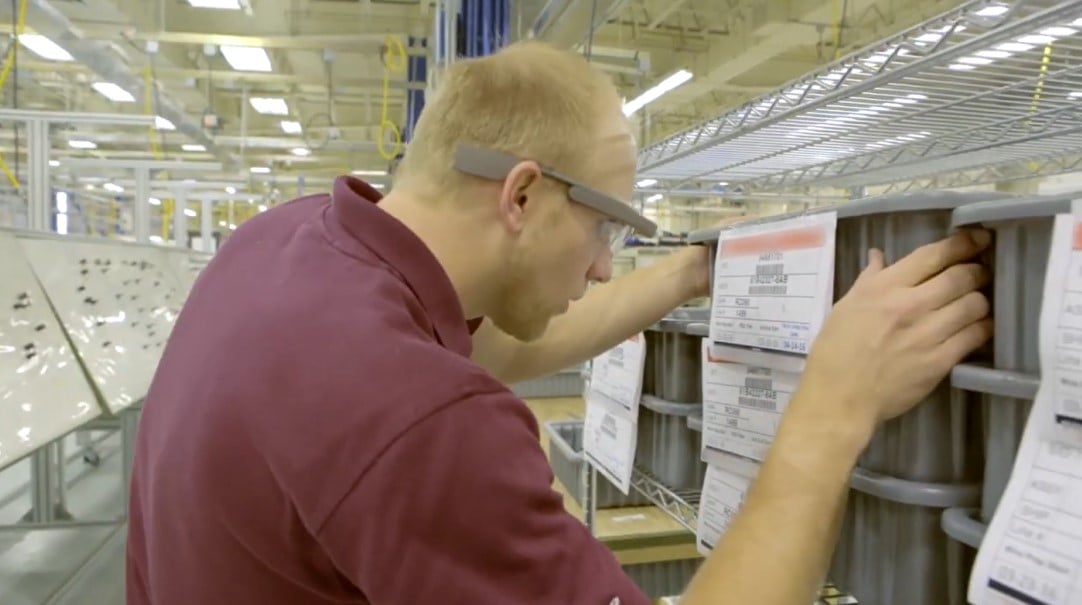
AI and OCR for Label and Packaging Verification
Optical Character Recognition (OCR) is an AI technique used to read and understand text or codes from physical documents. It can also be used for quality control by reading and verifying labels and serial numbers from product packages. By creating a system that automates the process, companies can better follow packaging compliance and regulations.
Using deep learning methods, OCR systems accurately interpret diverse fonts, sizes, and orientations on labels. For instance, it can be used to detect products that have expired, making sure only fresh products reach the shelves.
In car manufacturing, warning labels are crucial for letting consumers know about the safety features and potential hazards associated with the vehicle. AI and OCR can automate the process of checking such labels. Yamaha Motors implemented an AI-powered vision solution to automate the inspection of warning labels on their all-terrain vehicles (ATVs) and recreational off-highway vehicles (ROVs). Before using OCR, Yamaha checked labels manually, which took a lot of time. With AI, they were able to instantly verify label placement and content, making inspections faster and more accurate.
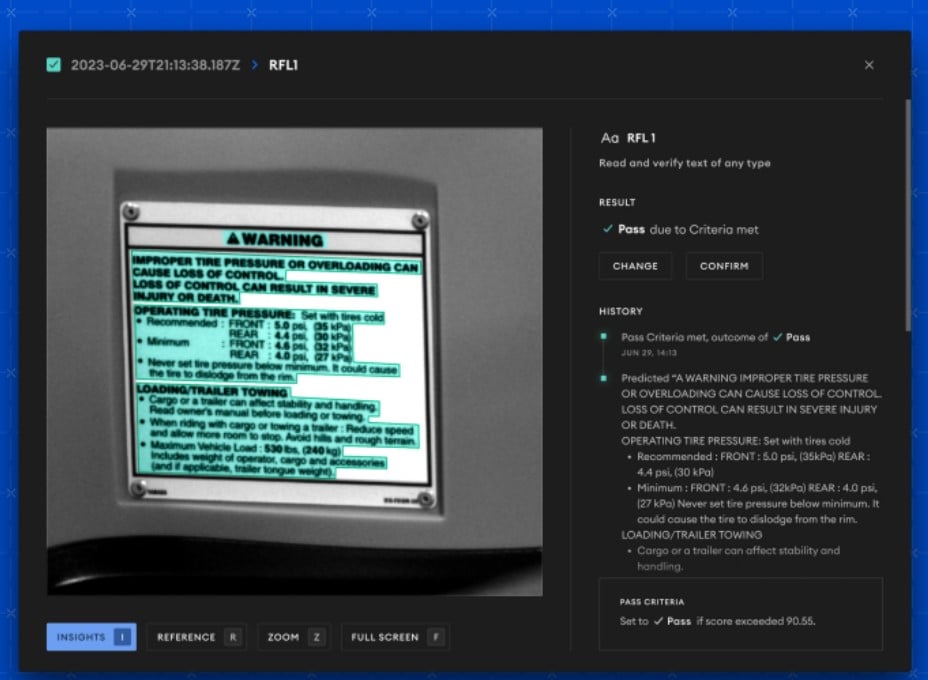
Structural Inspections for Safety Monitoring Using AI
Aerial drones that are integrated with AI and computer vision can be used to make infrastructure inspections faster and safer. They provide accurate assessments of buildings and bridges. Performing these tasks manually can be hazardous for human inspectors. These AI drones provide a much safer option. They can easily analyse structural integrity, identifying potential risks before they become critical.
Drones can be integrated with models that support advanced image classification and segmentation techniques to detect cracks, material degradation, and other structural weaknesses that might have been difficult to spot. By capturing high-resolution images and processing them through AI algorithms, they provide detailed defect analysis with a level of accuracy that would’ve been difficult with traditional methods. Such a level of accuracy is vital for many applications, especially in areas like power grid maintenance.
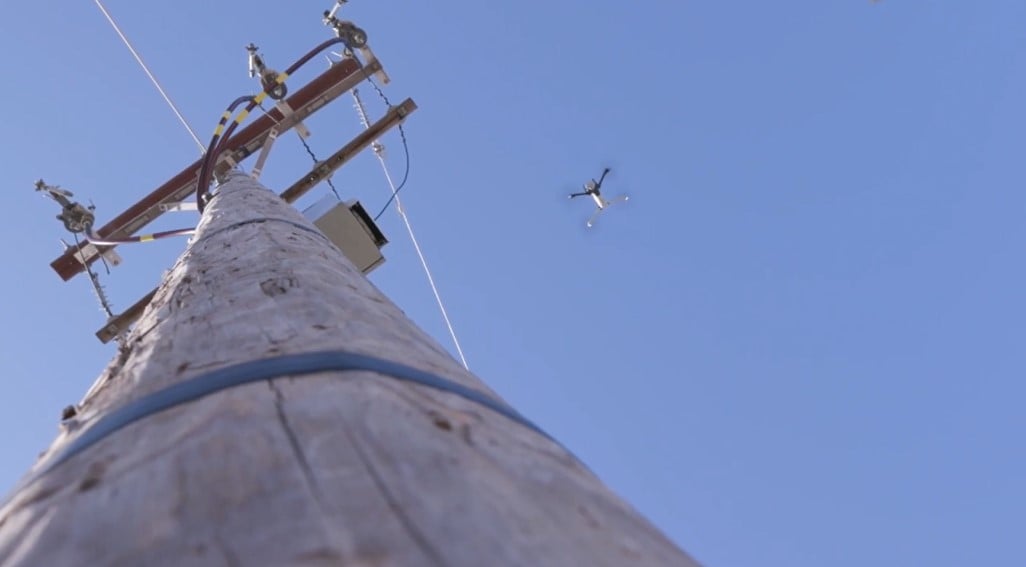
For example, a leading U.S. energy provider, ComEd, integrated AI drone inspections into its grid management and maintenance system. ComEd’s drones capture high-resolution images of power poles and critical infrastructure. Then, AI algorithms analyse these images and identify potential defects with over 95% accuracy. This automation has made grid inspections more reliable and reduced safety risks for workers. Using AI for inspections has also helped ComEd boost its net revenue, proving how cost-effective AI can be for monitoring structures and predicting maintenance needs.
Future Trends in AI Quality Control
It is likely that in the future, AI and the Internet of Things (IoT) - a network of interconnected sensors and devices - will drive quality control. Factories are already using AI-powered analytics and sensor data to detect defects, predict failures, and adjust operations in real-time. Right now, 54% of businesses use AI, and 51% use IoT, showing a growing shift toward automated and self-improving production systems.
For example, instead of using a traditional camera that records images for later review, factories are using IoT cameras that stream high-resolution images continuously. While a cloud camera also offers real-time monitoring by sending data to remote servers for processing, it relies on a stable internet connection. In contrast, an IoT camera typically processes data locally, which makes faster decision-making possible.
What We Can Offer as Technolynx
At Technolynx, we develop customised AI solutions for various applications like quality control and maintenance that help industries achieve higher accuracy, efficiency, and reliability. Our expertise surrounds creating applications using cutting-edge technologies like computer vision, generative AI, and XR.
We believe in developing ethical AI solutions that make your industrial processes more efficient. If you’re looking to enhance your quality assurance strategy with AI, we’re here to help. Reach out today!
Conclusion
AI and computer vision make quality control and maintenance faster and more accurate. They help spot defects quickly and reduce mistakes by automating inspections with innovative models. In particular, these solutions can cut waste and improve production efficiency.
AI can also be used to predict equipment issues before they happen, preventing breakdowns and reducing downtime. Technologies like generative AI and XR-based inspections help businesses maintain high quality while saving money.
As industries automate, using AI for quality control isn’t just an option; it’s crucial for staying competitive and ensuring long-term success.
Sources for the Images
BMW Group Press, 2019. Fast, efficient, reliable: Artificial intelligence in BMW Group Production. BMW Group
ComEd, 2024. ComEd UAS (Drone) Demo with Skydio. YouTube
Elementary, 2023. BMD-44_elementary_x_Yamaha_Case_Study. Elementary
Freepik. n.d. Futuristic technology concept. Generated by AI
JourneyApps, 2022. 8 Computer Vision Use Cases in Manufacturing. JourneyApps
Upskill, 2019. Boeing works with Upskill to Cut Production Time by 25%. YouTube
References
Airbus, 2016. Airbus Group Unit Testia to Supply Augmented Reality System to Spirit AeroSystems. 11 April.
Automotive Manufacturing Solutions, 2025. Audi is Advancing Vehicle Production with AI-Powered Image Processing. 4 February.
BMW Group Press, 2019. Fast, Efficient, Reliable: Artificial Intelligence in BMW Group Production
Capgemini, 2018. Augmented and Virtual Reality in Operations
Elementary, 2023. AI-Powered OCR for Label Inspection at Yamaha Motors
GlobeNewswire, 2024. AI Quality Inspection Market Report 2024: Forecasts to 2029. GlobeNewswire, 18 November.
Google Cloud, 2021. Google Cloud Manufacturing Report 2021
Kaspersky, 2024. More than Half of Companies Use AI and IoT in Their Business Processes. 29 February.
Manu, 2024. XR, VR, AR, and AI Report of 2024: Innovations and Opportunities for Businesses. Yord Studio, December.
McKinsey & Company. Smartening Up with Artificial Intelligence
Optelos, 2024. ComEd Case Study: Automating Grid Analytics Through Drone Power Line Inspection and Computer Vision AI. 11 April.
Precedence Research, 2024. Generative AI in Manufacturing Market Size, Share, and Trends 2024-2034. 14 October.